Brazzale S.p.A.

Request information or advice now
The project numbers
250.000 LUs
Storage capacity
8.000 sqm
Surface area
Cheese weels
Storage unit
Requirements
The constant growth of production has led to the need to create a new plant dedicated to maturing. In addition to seeking the location with the ideal microclimate, the Brazzale family was determined to invest in a plant at the cutting edge of technology, maintaining the highest standards of safety and reliability.
Our solutions
We have built the largest fully automated curing warehouseiamo.The project, realized in collaboration with Elten and Gran Mag, is developed in an area of 8,000 square meters in Cogollo del Cengio just 8 km from the Zanè site. The construction of a multi-depth plant has made it possible to reduce by 50% the area occupied for the storage of 250.000 forme di Gran Moravia cheese weels, equivalent to 10,000 tons of product. The 8,500 mini-racks of 32 shapes each are moved by shuttles, satellites and induction shuttles, achieving maximum levels of flow optimization and surface optimization.
The shuttles transport the mini-rack to the loading/unloading area from the warehouse where an induction shuttle transports them to the automatic brushing and returning area where 4 anthropomorphic robots operate.
The Bi-Bloc structure, in addition to the handling system, also integrates the ventilation system. Thanks to the 140 km of ducting of the ventilation and air conditioning system for the control of temperature and humidity, an excellent maturing process is guaranteed.
‘Artificial intelligence does not really exist, there is human one, and this plant is a wonderful example of it, An authentic wonder. To make it possible were the hands and minds of those formidable Italian and foreign technicians with whom I had the honor to spend a lot of time in the last year’, says Roberto Brazzale, Group Chairman. ‘The Warehouse will be filled in a few months, as all new production will be stored there, allowing us to recover many costs related to the seasoning third and save about 200,000 km of travel to and from the 15 warehouses currently used’.
Gallery
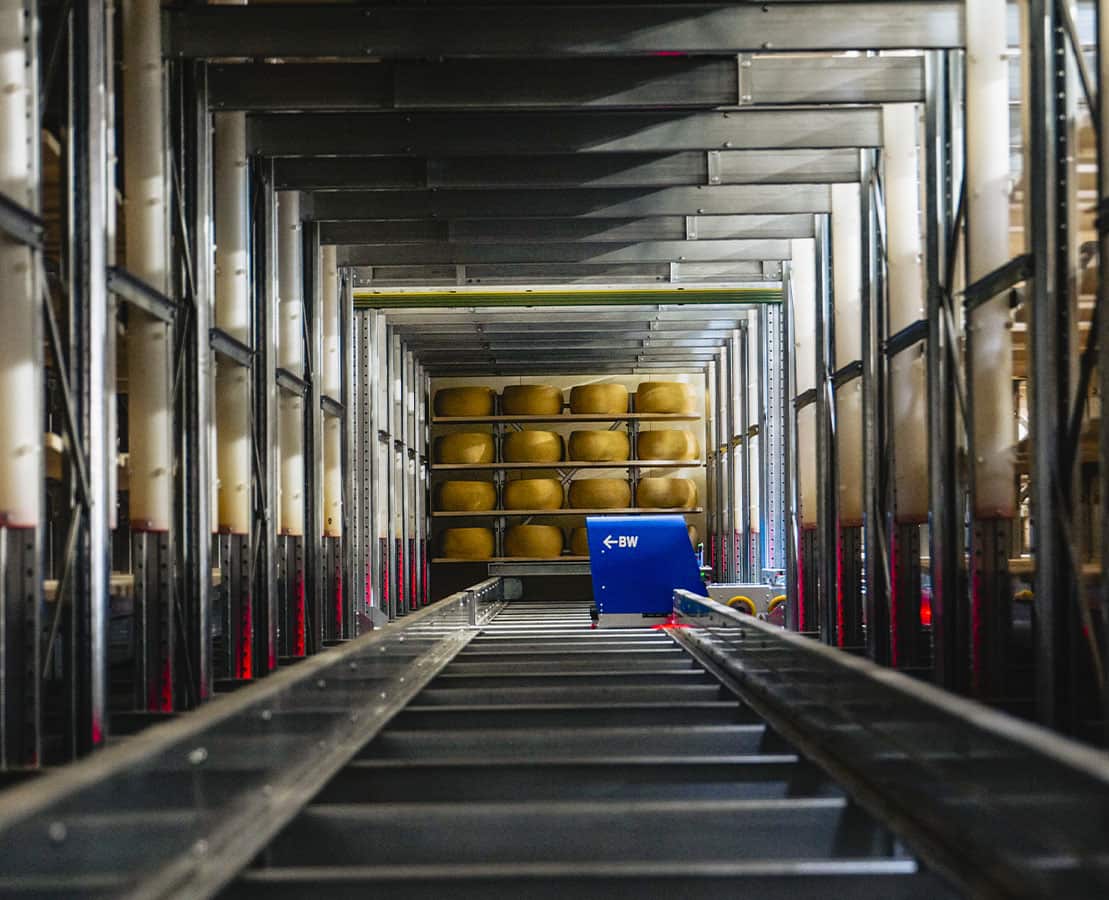
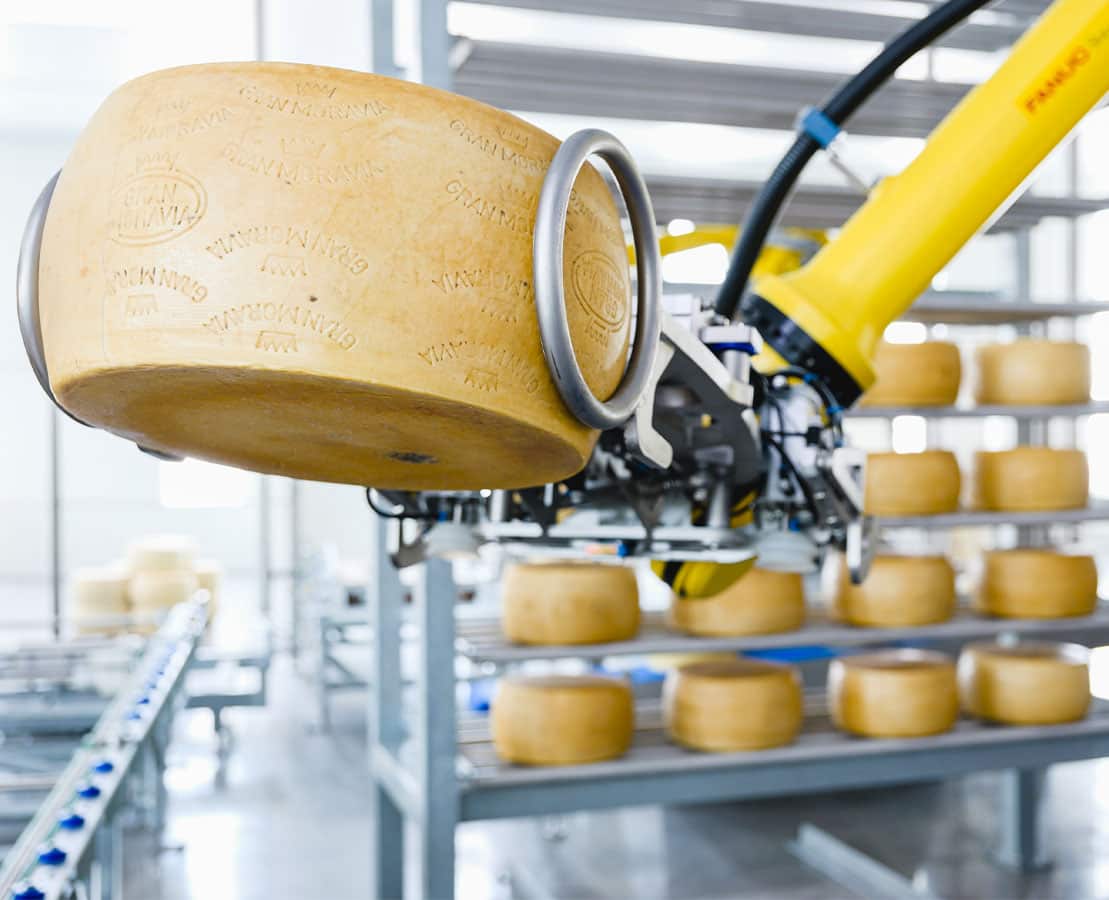